Antimony and tin recovery from secondary lead processing
Agenda for
25-27 June
2025
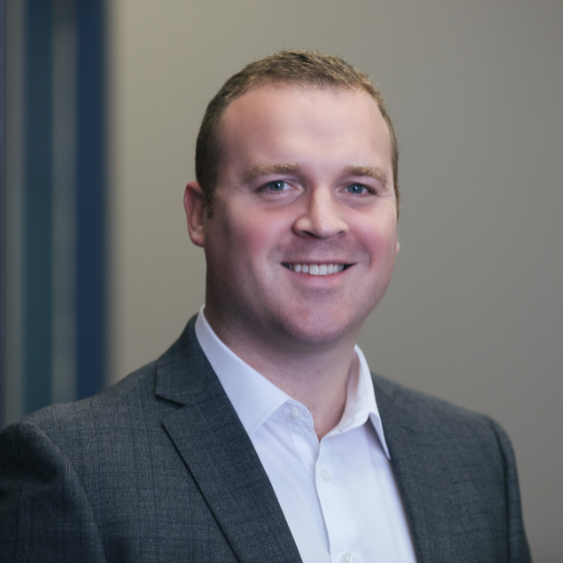
With recent supply chain uncertainties and price risk around these critical metals, we take a fresh look at the economic and strategic drivers around their recovery in the lead-acid battery supply chain. This presentation looks at options and opportunities for their processing within the lead industry, both leveraging existing assets and new technologies. One innovation discussed is the SCRUM process developed at Gopher Resource which delivers 99+% recovery of tin and antimony from end slags and byproducts.
Bio
Joseph Grogan is Chief Technology Officer at Gopher Resource, one of the largest lead battery recyclers in North America, producing over 300,000 tons of lead alloy per year. At Gopher, he leads growth and development efforts with focus on recycling batteries safer, more productively, and with a lower environmental footprint. Joe has spent his 18-year career working globally in the recycling and mining industries. He received his PhD in Metallurgical Engineering from the Colorado School of Mines, USA, his masters in Minerals Engineering from the Camborne School of Mines, UK, and his undergraduate degree in Geochemistry from University College Dublin, Ireland. In his free time, he enjoys playing music and coaching youth rugby.